Le Green & Lean, une philosophie
pour la “transition” ?
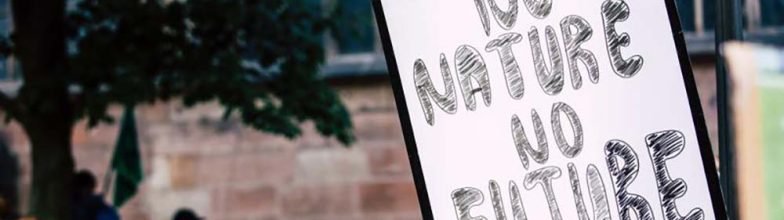
Le lean peut-il être le socle d’une nouvelle philosophie et de nouvelles méthodes et outils qui permettraient de concilier respect de la nature et rentabilité ?
Le Lean naît dans un contexte de croissance infinie…
Le Lean apparaît chez Toyota dans les années 50 alors que la concurrence internationale fait rage, que la trésorerie du constructeur automobile japonais est à sec, et qu’il dispose de moyens industriels limités. Toyota décide alors de réduire au strict minimum le temps qui s’écoule entre le moment où un client passe une commande et le moment où il règle sa facture. Le Lean est né !
Ses principes fondateurs (les 5 piliers) sont toujours d’actualité :
- Se mettre à la place du client et mesurer la valeur ajoutée client
- Mesurer les non-valeurs ajoutées pour en faire des leviers d’amélioration
- Observer le temps d’écoulement (ou Lead Time), le tendre et le maîtriser
- Mettre l’humain au centre de tout, utiliser les talents non exploités
- Penser amélioration continue (et infinie)
Ce contexte (offre plus forte que la demande, guerre des prix, cycle de vie des produits extrêmement court, concurrence mondiale, …) s’est généralisé à la plupart des secteurs d’activité. Aujourd’hui, les entreprises les plus performantes appliquent de près ou de loin la philosophie Lean. Mais cette philosophie n’est valable que dans un contexte de croissance infinie de la consommation et des ressources planétaires. Or cette vision du monde est erronée…
..cette croissance infinie a un impact insupportable…
Depuis les années 70, Le GIEC (Groupe d’experts Intergouvernemental sur l’Evolution du Climat) alerte sur la finitude des ressources et sur le dérèglement climatique en cours. Ce dérèglement est dû en majeure partie à notre consommation d’énergies fossiles, fortement émettrices de CO2.
Le constat est clair et terrifiant : si nous voulons rester en dessous des +2° d’ici 2100 et permettre aux générations actuelles et futures d’avoir un avenir, nous devons mettre fin aux émissions anthropiques de CO2 d’ici 2050. En 2015, tous les états participant à la COP21 (Accord de Paris) ont validé la nécessité de tenir cet objectif.
De plus, les stocks d’énergies fossiles (pétrole, gaz, charbon,…) et de ressources (terres rares, métaux, …) sont non renouvelables (à l’échelle humaine) ce qui compromet leur accessibilité pour les générations futures.
20% du CO2 émis sur la planète est dû à l’activité industrielle et 20% au transport*.
D’un bout à l’autre de nos supply chains (de la matière première aux consommateurs), nos entreprises ont une responsabilité dans le respect de ces objectifs de dé-carbonation et de diminution de l’utilisation des ressources non renouvelables.
De nouveaux gaspillages sont à prendre en compte…
Le Lean, dans la mesure où il est basé sur la “chasse aux gaspillages”, peut se contenter d’intégrer ces nouveaux gaspillages de CO2 et de ressources non renouvelables.
Mais l’urgence climatique et environnementale est telle que ces nouveaux gaspillages ne peuvent être placés au même niveau que les autres.
Historiquement, les entreprises qui ont une démarche Lean “classique” commencent par des chantiers Lean sur leurs sites de production (cercle 1 et 2), les postes de travail, les lignes de fabrication, puis leurs supply chain internes (modes d’approvisionnement, gestion des stocks, Lean “Warehousing”) et les services proches des sites (qualité, BE, maintenance,…). Elles cherchent ensuite à accompagner leurs fournisseurs dans la mise en place d’une démarche Lean (cercle 3) et finissent par s’attaquer aux produits et au business model (analyse de la valeur, agilité, …) (cercle 4).
Cette démarche est logique car les gains financiers les plus rapides se trouvent souvent au pied des lignes de production. Le schéma suivant traduit bien la logique actuelle des démarches Lean.
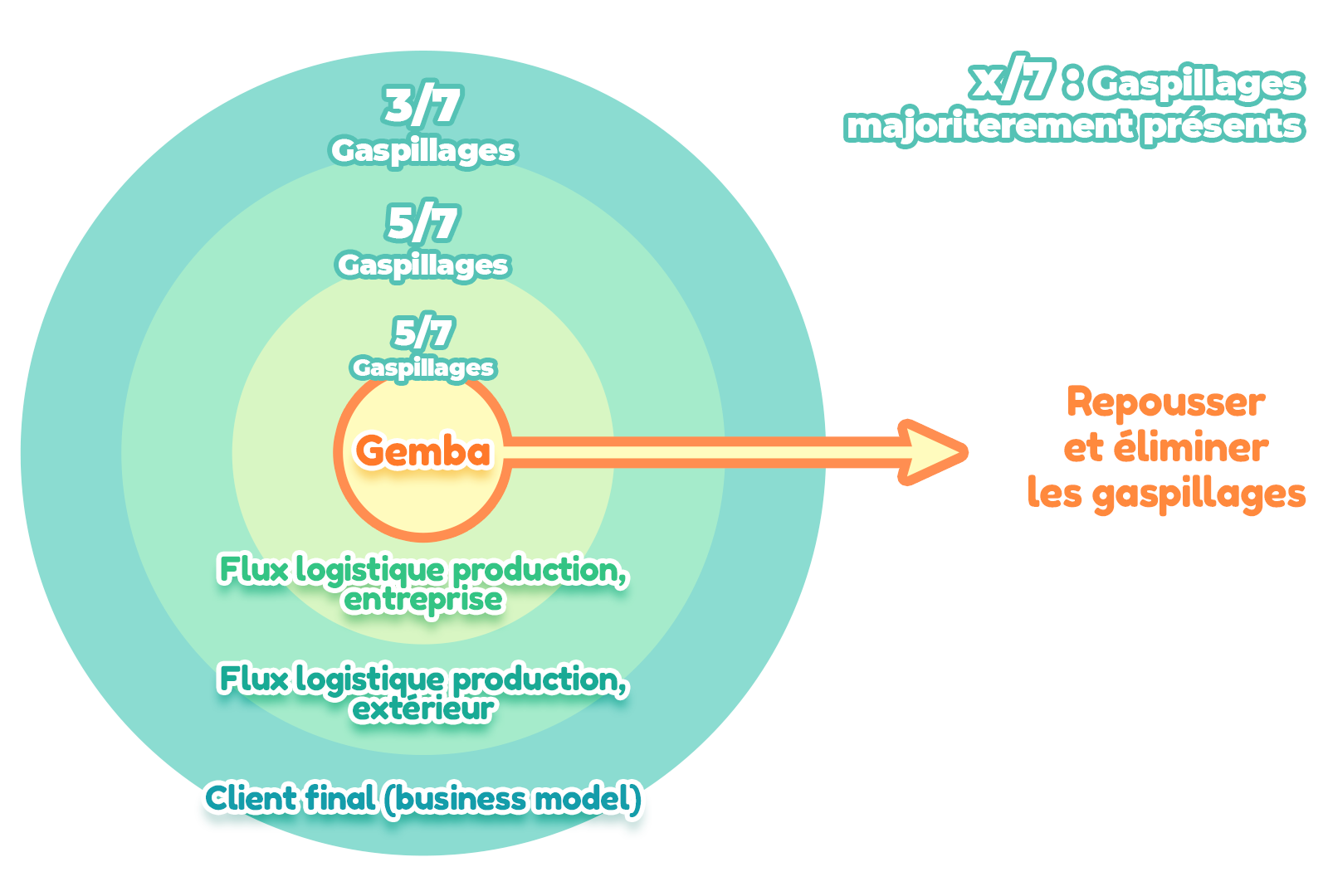
…et ils doivent primer sur tous les autres !
Si la performance des entreprises reste nécessaire – voire même indispensable- dans une période de contraction comme celle que nous vivons, l’urgence environnementale est telle que les gaspillages “écologiques” doivent primer sur tous les autres et que cette performance ne peut avoir lieu au détriment de la nature.
Il semble nécessaire de repréciser les gaspillages du Lean en prenant en compte leur impact environnemental qui vient parfois à l’encontre de leur impact sur la performance économique.
Prenons l’exemple d’une usine qui fabrique des drones comme dans la 7-Shapes School (Le secteur d’activité influe beaucoup !) et voyons comment ré-analyser les 7 gaspillages en prenant en compte l’impact environnemental :
Gaspillage Lean | Impact environnemental | Exemples | Actions décarbonation possibles |
1-Transport | +++ | Fournisseurs trop éloignés, tournées non optimisées, pas de moyen de transport décarboné ,… | Regroupement des commandes, produire local, micro usines,… |
2-Stocks | ++ | Stocks mal gérés, trop de références (diversité), matières non renouvelables,.. | Les 5 R : refuse, reduce, recycle, reuse, rot standardiser les ref. (voir dév. produit et BE) |
3-Mouvement au poste | + | Moyens utilisant trop d’énergie, automatisation à outrance,… | Utiliser la gravité, énergie verte, faire simple (moins de ref.),… |
4-Attente | ++ | Conso d’énergie même quand la machine ne tourne pas | Start & stop, 0 conso si 0 produit, politique de regroupement de commandes (donc j’attends plus !) |
5-Sur production | +++ | Production inutile, trop de déchets, pas de réparabilité du produit,… | 5R et notamment : réparer plutôt que de reproduire |
6-Processus inutiles | + | Trop de papier, démarche “digital & responsable”,…Trop de déchets | Optimisation logiciel, serveurs en local, 5S des bases de données,… |
7-Défauts | ++ | Déchets, matières, énergie utilisée pour rien,… | Compter l’énergie perdue, valorisation des déchets,… |
8-Gaspillage humain | ++++ | Personnel pas formé, pas au courant de l’impact de son travail et pas au courant de son impact potentiel en tant que citoyen/consommateur | Formation de tous les salariés à la crise environnementale en-cours |
On voit dans ce tableau que les gisements de gaspillage ne sont plus directement dans l’entreprise mais dans l’ensemble des cercles. On voit également que ces nouveaux gaspillages s’opposent parfois à la chasse aux gaspillages “traditionnels”. C’est ainsi que le Lean “traditionnel” avait favorisé la délocalisation pour des raisons d’efficacité liée à la spécialisation des sites, et aussi parce que les coûts de transports étaient négligeables.
La prise en compte de l’impact environnemental de ces transports coûteux en carbone pourrait amener à re-localiser massivement. Quoique ? Cela s’analyse ! C’est un sujet complexe et nous ne voudrions surtout pas tomber dans le piège de la simplification à outrance…
Du coup, le cercle le plus puissant ne serait-il pas celui qui consiste à former tous les salariés à la situation ? La prise de conscience de tous n’est-elle pas la solution pour appréhender la complexité du sujet et mettre enfin l’intelligence collective en marche ?
Seule une vision systémique, globale, et un élan de toutes les parties prenantes, du client aux fournisseurs en passant par les collaborateurs peut permettre à nos entreprises de se transformer à la hauteur des enjeux.
Les 6 principes clés du Green & Lean
De ces constats, nous proposons de qualifier ce nouveau Lean de Green & Lean et de faire évoluer les 5 principes du Lean en 6 principes :
- 1er principe et le plus important : le respect de la nature.
- 2ème principe : mettre le besoin de son client au centre de son entreprise => un client responsable !
- 3ème principe : chasser les gaspillages, la non valeur-ajoutée => éliminer les produits/process non compatibles avec le respect de la nature puis chasser la non-valeur ajoutée pour les clients
- 4ème principe : tendre les flux pour réduire l’utilisation des ressources non renouvelables. Ensuite réduire les délais entre commandes et paiements
- 5ème principe : utiliser l’intelligence collective. => formation de tous les salariés à la Transition et au Lean.
- 6ème principe : mettre en place un processus d’amélioration continue de ces principes.
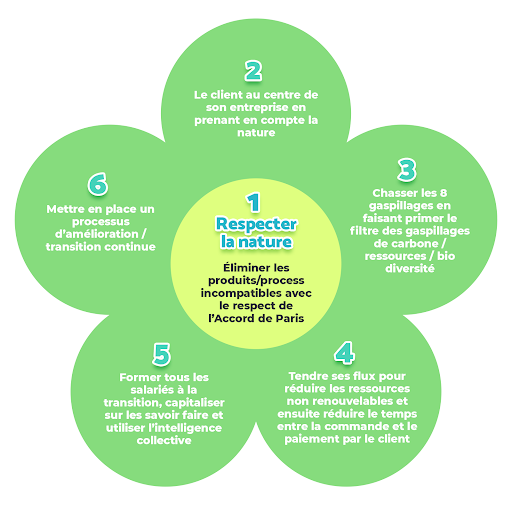
Conclusion : Le Green & Lean, la formation du citoyen / collaborateur d’aujourd’hui !
Il nous semble que tout le bon sens de la philosophie Lean et les puissants outils et méthodes qui en découlent peuvent être le socle d’une nouvelle philosophie basée sur le respect de la nature.
Cela passe par un véritable changement de paradigme : nous ne devons plus seulement penser à la compétitivité de nos entreprises, mais d’abord à leur contribution à la décarbonation du monde, et sur l’ensemble de l’analyse du cycle de vie**. Et seule l’intelligence collective, la collaboration de toutes les parties prenantes peut permettre de penser cette nouvelle économie. Alors, tous Green & Lean ?
Se former au Green & Lean chez 7-Shapes School
Nous proposons des parcours de formation au Lean basés sur un jeu de simulation d’entreprise.
Nous concevons actuellement un Parcours de formation Green & Lean qui, nous l’espérons, pourra servir de stimulant pour la mise en oeuvre d’une démarche de transition Green & Lean dans les entreprises.
Notre objectif est de sensibiliser et de former tout le monde à ce nouveau paradigme sociétal. CQFD
Notre volonté est de co-construire des scénarios de transition avec une communauté de transitionneurs. Alors, si ce sujet t’intéresse et que tu souhaites nous aider à créer ce Parcours Green & Lean, n’hésite pas à prendre contact avec nous !
Si tu as des réflexions, contradictions, propositions, suite à la lecture de cet article, n’hésite pas à nous en faire part en commentaire ou à ces adresses : fdoumic@seven-shapes.com ou juliencharles@seven-shapes.com
Pour être informé de l’avancement de notre parcours “Green & Lean”, c’est ici : https://www.7-shapes.com/parcours-lean-green-durable/
_________________________________
* Rapport du GIEC 2018
** Comme le montre bien aussi la thèse d’Alain Fercoq http://www.theses.fr/180718185 qui, dès 2014, montrait la dimension systémique de cette analyse carbone
Nos articles sur la performance
Lorem ipsum dolor sit amet, consectetur adipiscing elit.
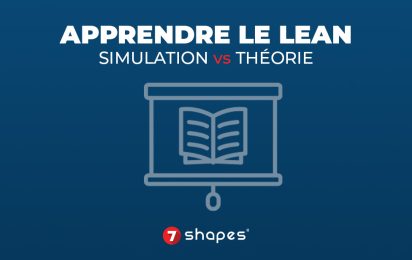
Apprendre le lean : simulation VS théorie
Le Lean Management est devenu un incontournable pour les entreprises souhaitant optimiser leurs processus et améliorer leur performance. Mais comment…
Lire l’article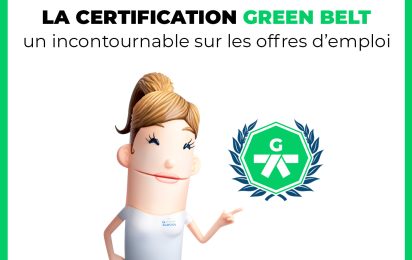
Certification Green Belt : un critère clé dans de nombreuses offres d’emploi
Dans un monde professionnel en constante évolution, la maîtrise du Lean Management est un véritable atout pour se démarquer. De plus en…
Lire l’article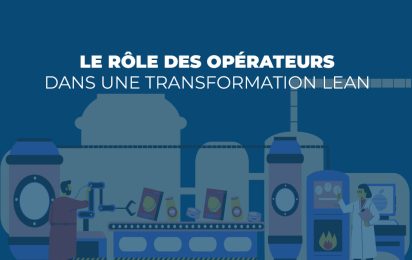
Le rôle des opérateurs dans une transformation Lean
Comment les entreprises peuvent-elles rester compétitives dans un monde en perpétuelle évolution ? Comment éliminer les gaspillages tout en créant…
Lire l’article