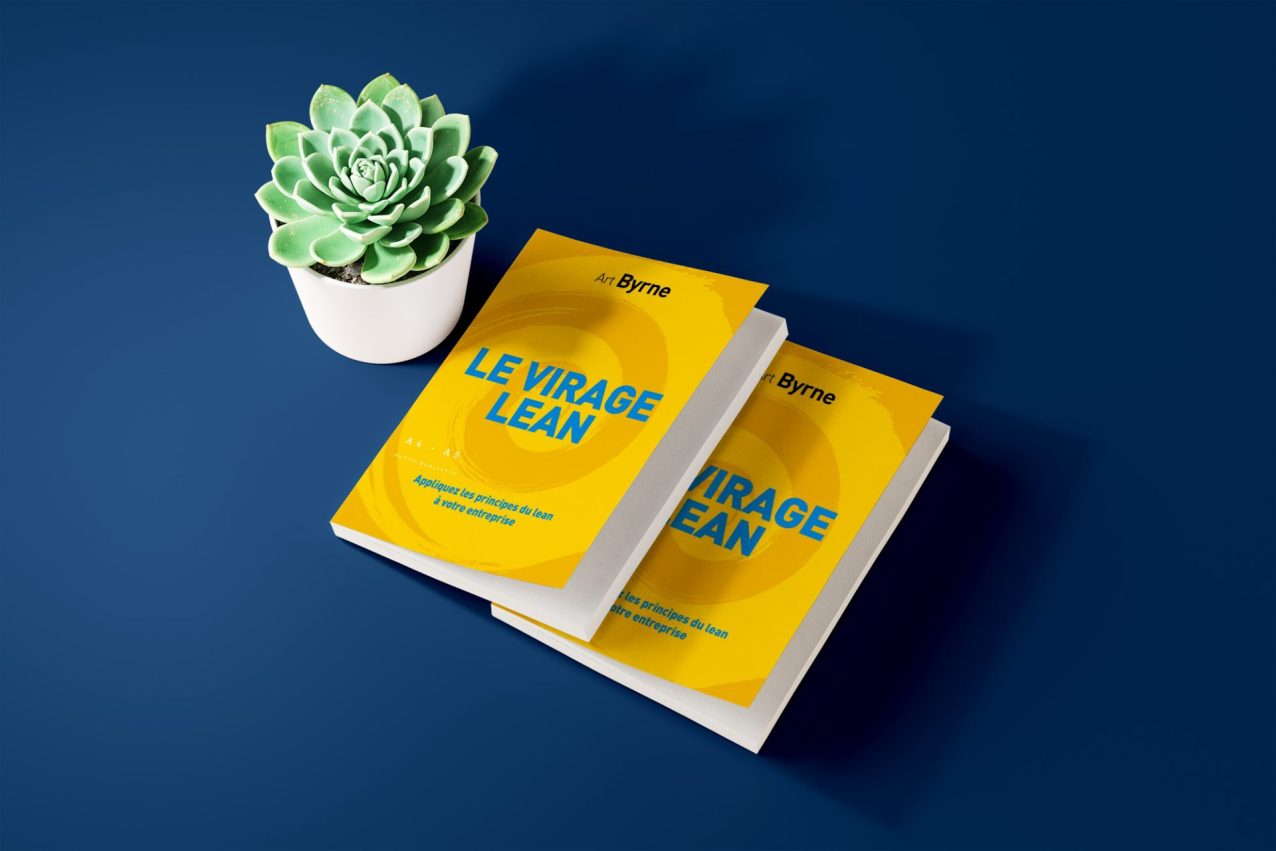
Le virage Lean – Résumé du livre
Dans cet article, nous résumons un livre qui, pour nous, est un indispensable dans le milieu du Lean Management. Écrit par un américain Art Byrne, ce livre va droit au but et est écrit de manière simple, limpide et efficace. Avec lui, le Lean semble…
Lire l'article