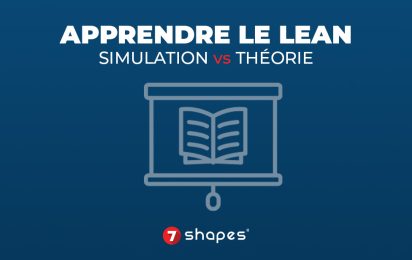
Apprendre le lean : simulation VS théorie
Le Lean Management est devenu un incontournable pour les entreprises souhaitant optimiser leurs processus et améliorer leur performance. Mais comment…
Lire l'articleLe Lean Management est devenu un incontournable pour les entreprises souhaitant optimiser leurs processus et améliorer leur performance. Mais comment…
Lire l'articleDans un monde professionnel en constante évolution, la maîtrise du Lean Management est un véritable atout pour se démarquer. De plus en…
Lire l'articleComment les entreprises peuvent-elles rester compétitives dans un monde en perpétuelle évolution ? Comment éliminer les gaspillages tout en créant…
Lire l'articleDans un environnement où la performance et l'innovation dictent le succès, maîtriser le Lean Management et le management visuel n’est…
Lire l'articleLe Takt Time est une mesure cruciale en production qui détermine le rythme auquel un produit doit être fabriqué pour…
Lire l'articleDans cet article, vous retrouverez la présentation de 3 outils pour bien cadrer et planifier vos projets Lean Management. Quels…
Lire l'articleDans cet article, nous allons explorer les différences entre les certifications Lean : White Belt, Yellow Belt, Green Belt et…
Lire l'articleCartographie de la Chaîne de Valeur : le temps de traversée (Lead Time) et le pourcentage de valeur ajoutée (également…
Lire l'articleLe Lean Management, ça vous dit quelque chose ? Cette approche d'organisation, réputée pour transformer les entreprises en véritables machines…
Lire l'article