Identification de problème,
comment faire ?
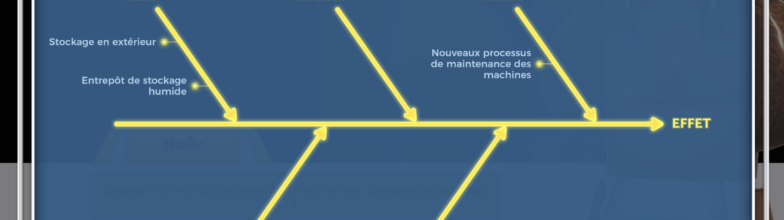
“Un problème sans solution est un problème mal posé” disait Einstein. C’est plein de bon sens, n’est-ce pas ? Dans le Lean Management (mais on peut l’appliquer à la vie en général), avant de trouver une quelconque solution, il est primordial de s’intéresser au problème en profondeur afin de pouvoir trouver la cause racine. Et pour cela, il faut se déplacer sur le terrain et utiliser le Gemba Walk (ou tournée terrain). C’est la base !
Pour ceci, nous pouvons utiliser 3 méthodes. Toutes ne viennent pas du Lean, mais combinées ensemble, elles permettent de comprendre le problème avant de réfléchir à une solution ! C’est ce qu’on peut appeler “l’identification de problème”.
Le QQOQC
Première méthode et première étape de l’identification de problème. Le QQOQC permet de poser le contexte du problème et d’en définir un périmètre via 5 questions :
- Qui ? M’a informé du problème et qui est concerné ?
- Quoi ? Qu’est-ce qui caractérise la situation ? Quel est le problème qui est constaté?
- Où ? Le problème s’est-il produit ?
- Quand ? Quelle heure, quel jour, pendant combien de temps, à quelle fréquence ?
- Comment ? Cela se manifeste-t-il ? Comment avons-nous pris conscience de ce problème ?
Une fois que l’on a définit les éléments de contexte, on peut passer à la suite et aller plus loin !
Les 5M
Cette seconde méthode porte différents noms : diagramme Causes-Effets, diagramme d’Ishikawa, 5M ou diagramme en arêtes de poisson. Elle est utilisée pour aller plus loin dans l’identification du problème et permet de les lister de façon visuelle.
Pour construire le diagramme d’Ishikawa, il faut s’interroger sur le problème depuis 5 points de vues différents et classer les causes potentielles en 5 catégories (les 5M) :
- Matière : les causes liées aux matériaux ou matières premières utilisés
- Matériel : les causes liées aux machines et outils utilisés
- Méthode : les causes liées à la qualité des processus mis en place, à la recherche et développement, à la qualité des instructions au poste de travail.
- Main-d’oeuvre : les causes liées à l’humain (défauts de formation, absence…)
- Milieu : les causes liées à l’environnement (température, humidité…)
Petit rappel : On peut appliquer cette méthode et ce diagramme à n’importe quel problème rencontré, quelque soit le milieu dans lequel il intervient (atelier de production, service, magasin logistique…) !
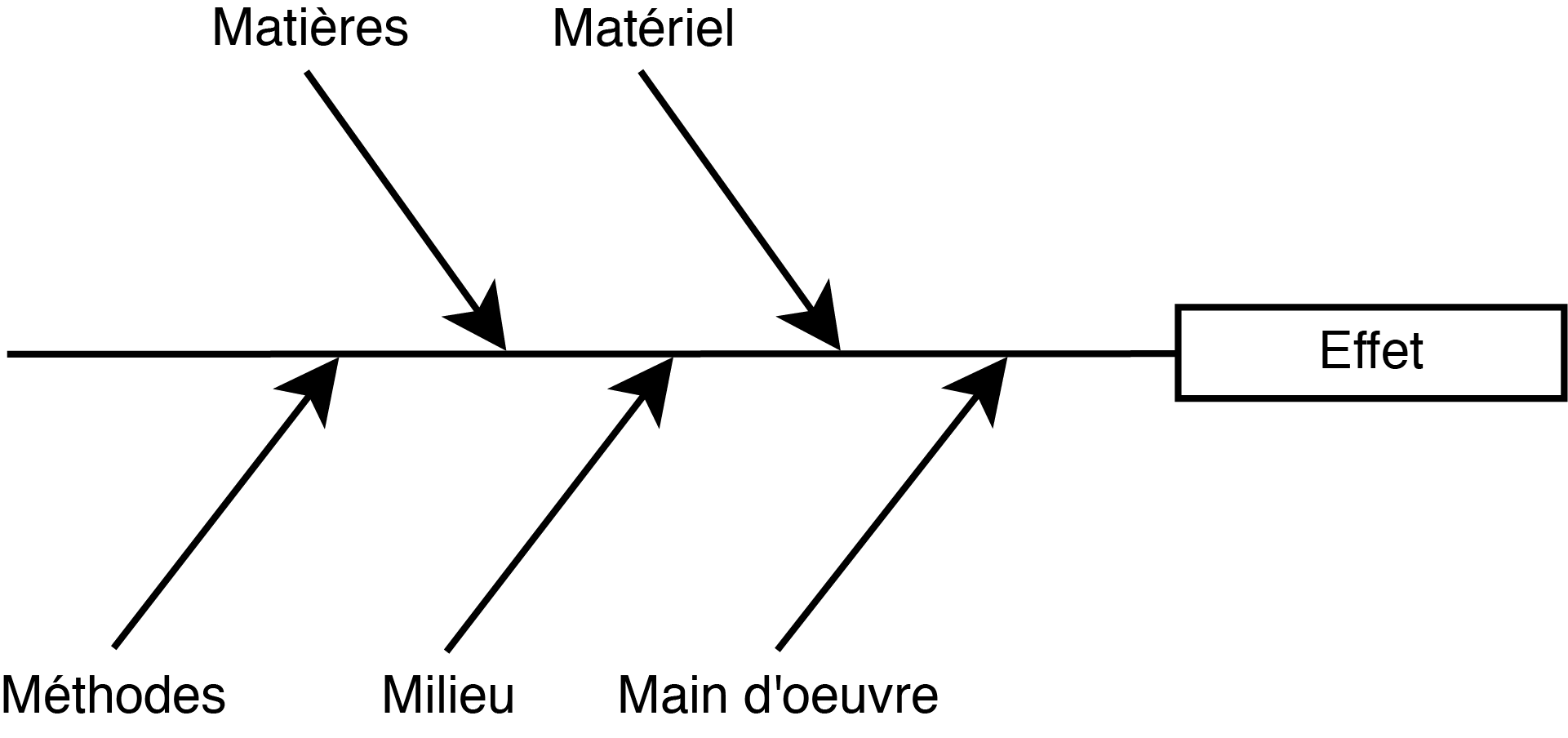
Les 5P
Une fois votre catégorie de cause choisie, une dernière étape, le « 5 pourquoi ».
Il permet de mettre en évidence la cause racine. Ici, il ne s’agit pas de poser simplement 5 fois la question “Pourquoi”, mais plutôt de créer des questions pertinentes commençant par “Pourquoi” !
Exemple dans la School :
Problème – Effet : L’opérateur travaille 31% de son temps
- Pourquoi… L’opérateur ne travaille qu’à 31% du temps total ? Cause matière 1ère
- Pourquoi… n’a-t-il pas de composants (matières 1ères) ?
- Pourquoi ? Le logisticien ne passe pas assez souvent
- Pourquoi ? Il doit fournir 3 postes de travail
- Pourquoi ? Il est tout seul / fréquence trop faible
Parfois, s’arrêter au 3ème ou 4ème « pourquoi » peut suffire. Mais, la cause racine est très souvent plus profonde !
Et à la 7-Shapes School, comment ça se passe ?
L’identification de problème est un mini-jeu présent dans les parcours White, Yellow et Green Belt Manufacturing !
Le scénario de ce mini-jeu est basé sur un problème qualité dont il faut trouver la cause. Pour ceci, ces trois méthodes sont essentielles et permettent de trouver cette cause racine. Par la suite, elles vont permettre d’appliquer une solution adaptée. L’ensemble de ce mini-jeu est basé sur un Gemba Walk, qui permet de réunir suffisamment d’informations pour identifier la cause du problème en allant interroger les différents personnages de l’usine.
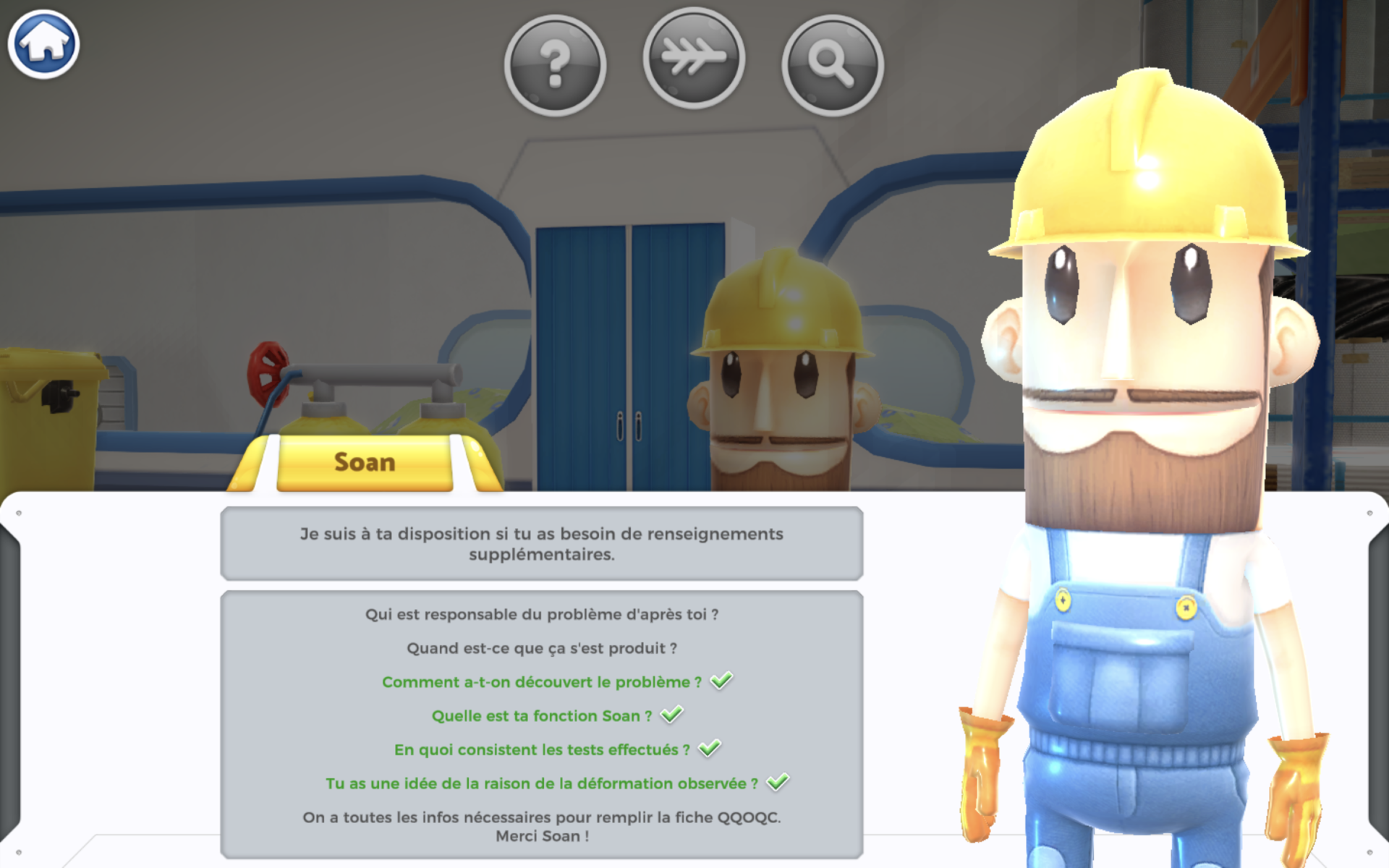
Au fur et à mesure du questionnement, on peut remplir la fiche QQOQC. Il permet de comprendre le contexte de l’apparition du problème.
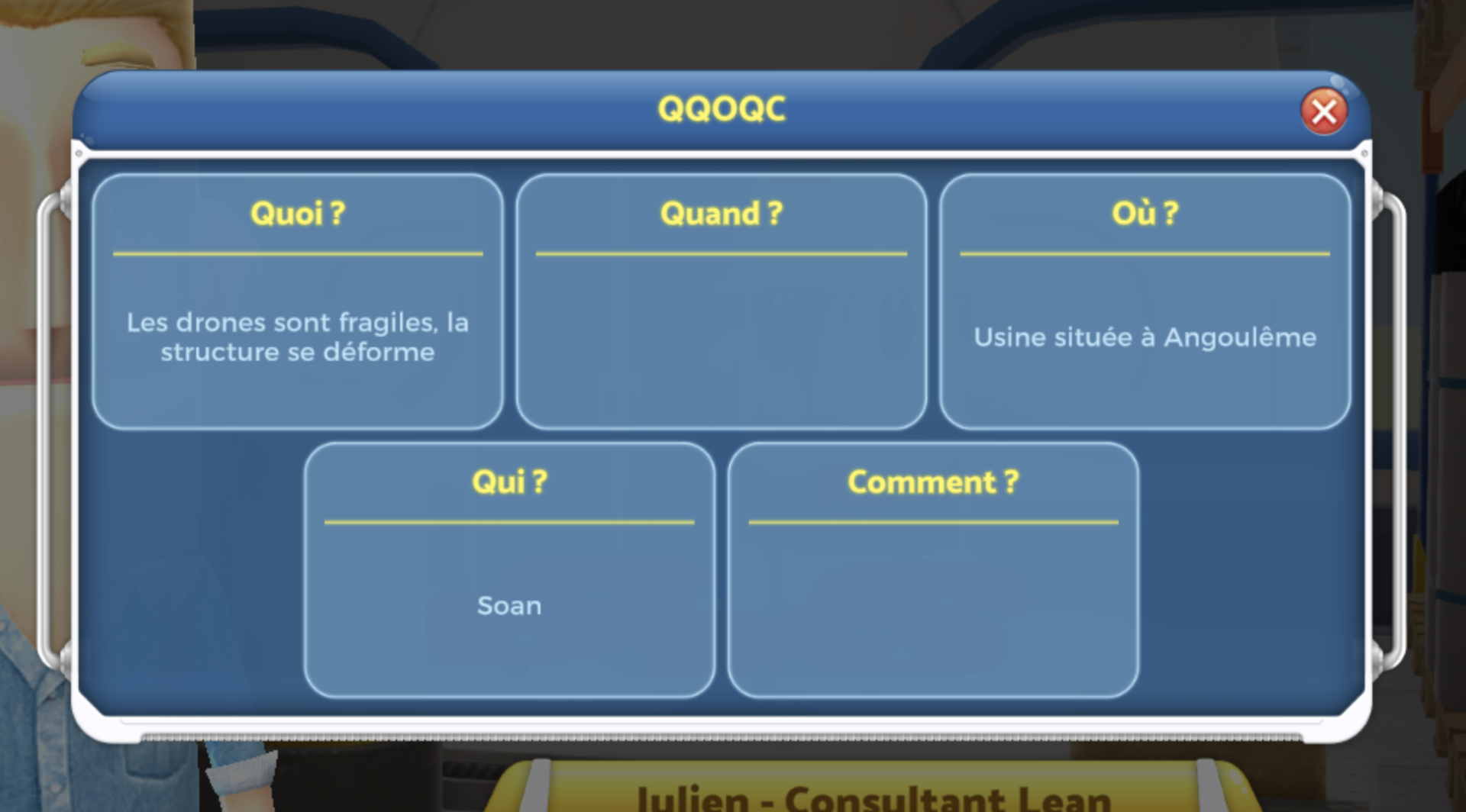
Ensuite, on cherche à remplir le diagramme d’Ishikawa en creusant plus en profondeur dans les causes potentielles du problème.
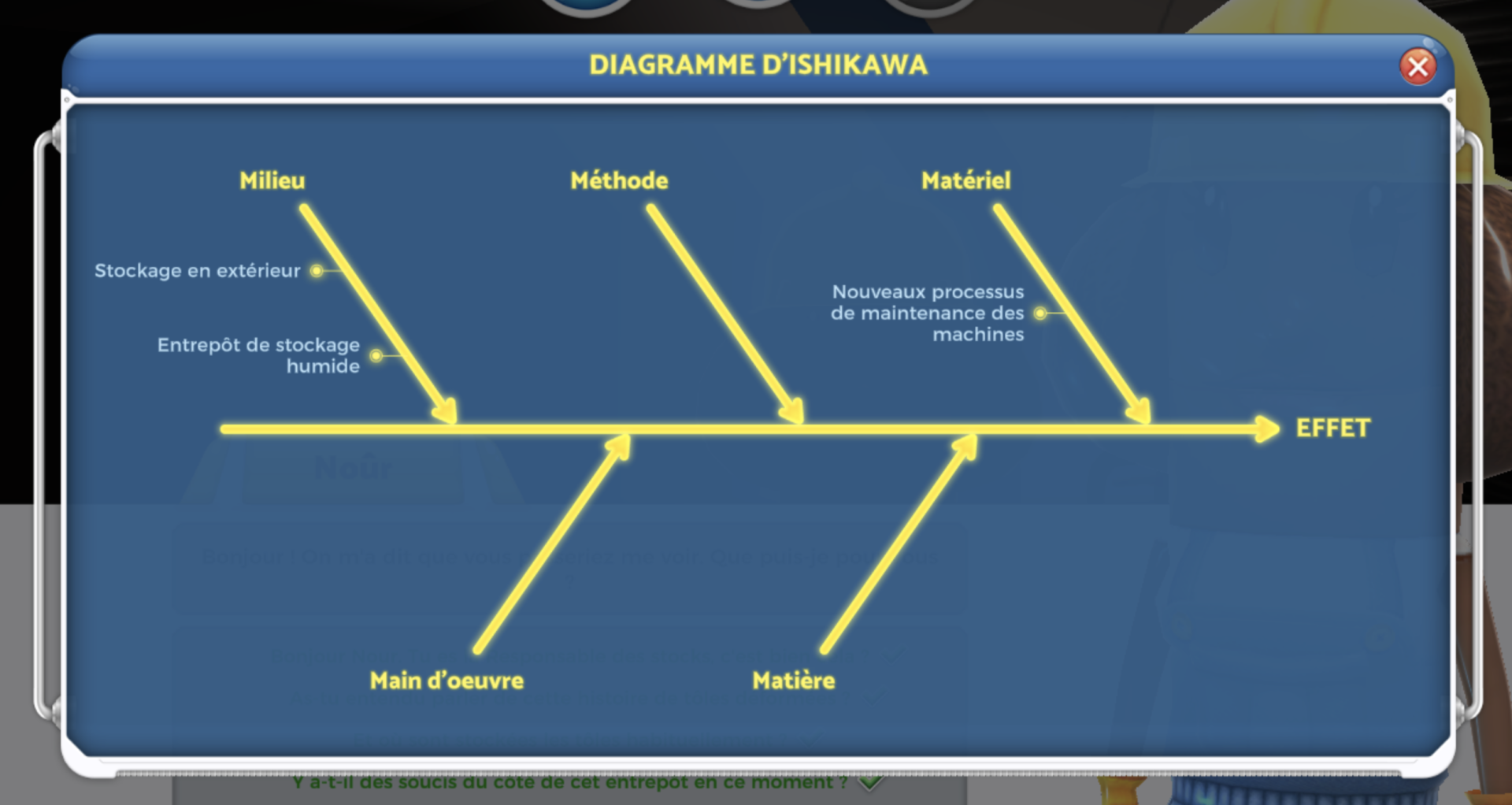
Puis, on essaie de supprimer certaines causes potentielles qui ne sont finalement pas liées au problème. Pour cela, on vérifie chacune de ces causes identifiées et on les élimine ou de les garde !
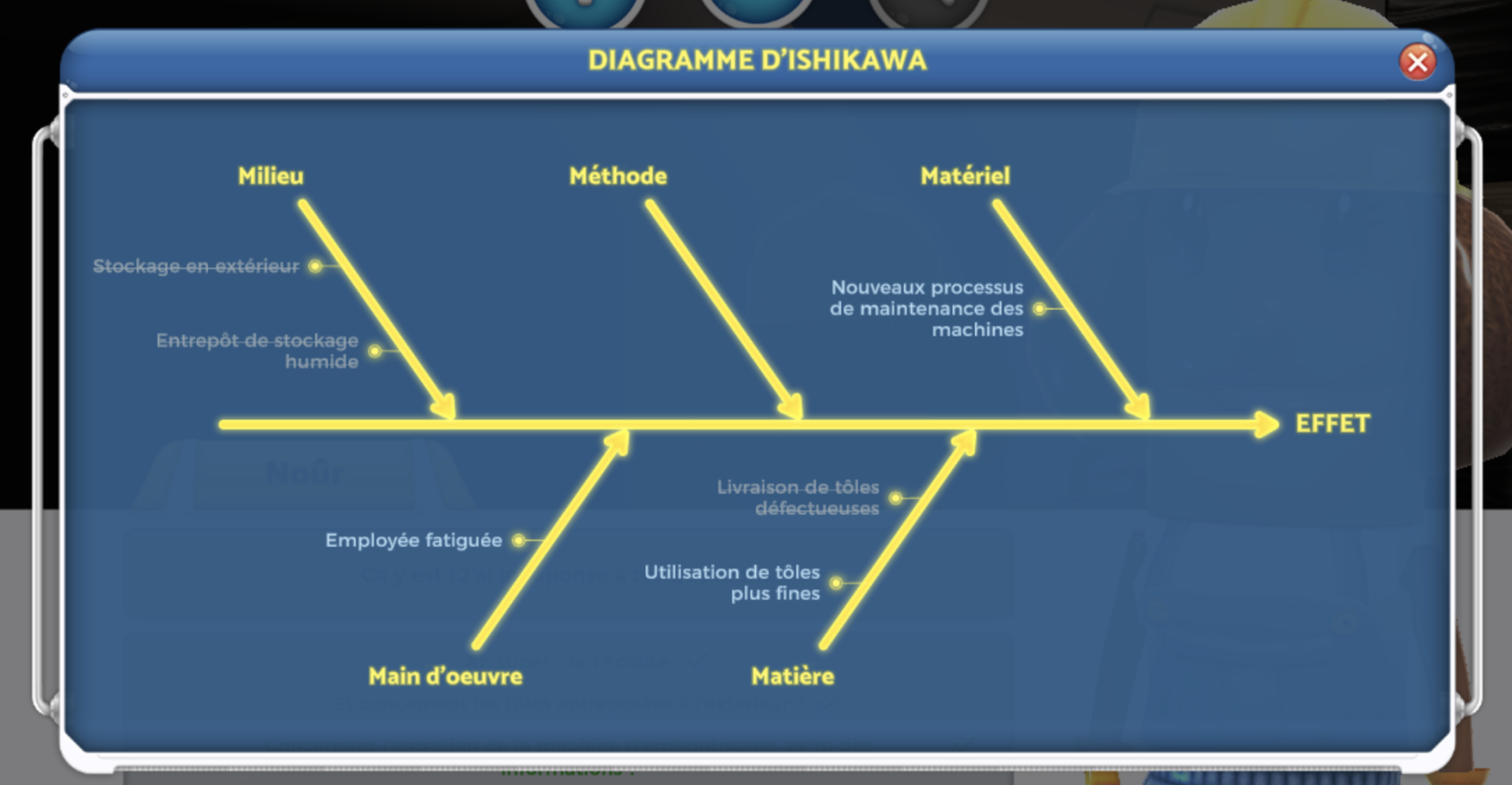
Enfin, on utilise les 5P en réunissant tout le monde et en faisant en sorte de poser les bonnes questions. Elles permettront d’arriver à identifier la cause racine.
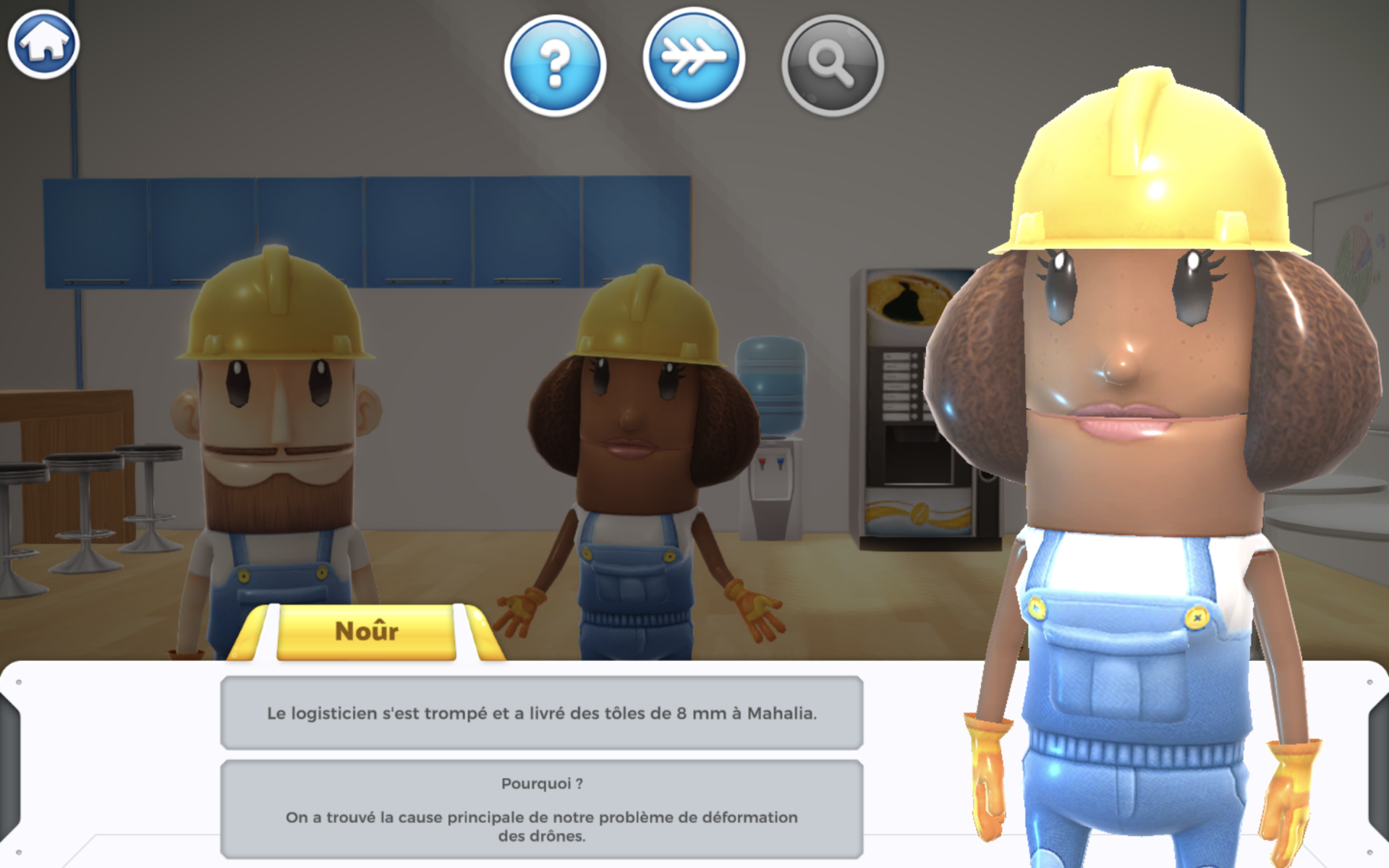
Chacun de ces outils peut être appliqué seul, à l’issu d’un problème sur le terrain, ou pendant une animation journalière de production. Un tableau blanc, un paper board, des post-it, des crayons et surtout un équipe, suffisent à pouvoir faire son premier chantier d’identification de problèmes sur le terrain.
Vous n’avez plus d’excuses !
À très vite à la 7-Shapes School ici
Nos articles sur la performance
Lorem ipsum dolor sit amet, consectetur adipiscing elit.
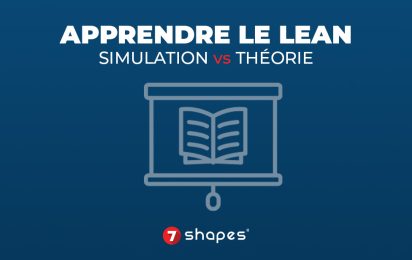
Apprendre le lean : simulation VS théorie
Le Lean Management est devenu un incontournable pour les entreprises souhaitant optimiser leurs processus et améliorer leur performance. Mais comment…
Lire l’article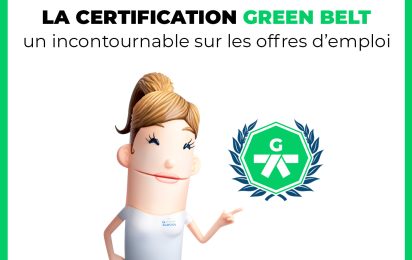
Certification Green Belt : un critère clé dans de nombreuses offres d’emploi
Dans un monde professionnel en constante évolution, la maîtrise du Lean Management est un véritable atout pour se démarquer. De plus en…
Lire l’article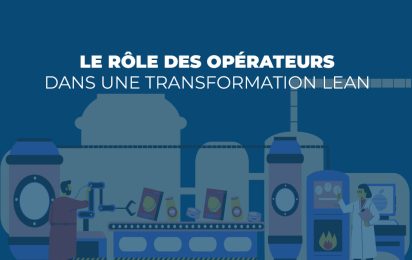
Le rôle des opérateurs dans une transformation Lean
Comment les entreprises peuvent-elles rester compétitives dans un monde en perpétuelle évolution ? Comment éliminer les gaspillages tout en créant…
Lire l’article